In the world of modern construction, Structural Insulated Panels (SIPs) are becoming increasingly popular due to their energy efficiency, strength, and ease of installation. But how are these panels made? The method of production can significantly impact both the final product and the economics of construction. Here, we delve into three distinct approaches to SIP manufacturing, including one innovative technique pioneered by our team.
1. Laminating Facility: The Traditional Approach
The most straightforward method for producing SIPs involves a laminating facility. Here’s how it works:
- Materials: You start by purchasing pre-made surface materials (like OSB or MGO) and core materials (typically rigid foam insulation like PIR or XPS).
- Process: Sheets of surface material are coated with adhesive, then the core is sandwiched between them. This assembly is then pressed under heat or at room temperature until the adhesive cures, forming a rigid panel.
- Advantages: This method is widely used because it’s straightforward, allowing for high-volume production. It’s ideal for both load-bearing and non-load-bearing applications due to its versatility in material choice.
- Output: Due to the simplicity of the process, laminating facilities can achieve high output rates, making it cost-effective for large-scale production.
2. Injection Method for Foam Cores
A slightly more sophisticated approach involves injecting foam directly into the panel:
- Process: Two surface layers are fixed with a gap in between. Liquid foam is injected into this cavity, expanding to fill the space (restrained rise). Once cured, it forms the core.
- Benefits: This method reduces material and transportation costs since you’re dealing with liquid foam that expands, rather than pre-formed foam blocks. It also allows for custom thicknesses of the core without needing to stock multiple sizes.
- Considerations: While this method can be more cost-effective, it requires precise control over the injection process to ensure uniform foam distribution and panel integrity.
3. Integrated Production Line: Our Innovation
Our team has developed a pioneering method where both the surface layers and the foam core are produced simultaneously:
- Process: In this setup, raw materials enter one end of the line, where they’re processed into surface layers. At the same time, foam is generated and injected between these layers as they move through the production line into the owen below.
- Output: Our specific setup can produce about 25 panels per hour, which translates into enough exterior wall panels for an average-sized American home (approximately 2,286 square feet) every two hours.
- Pros: This method gives us unparalleled control over the type, quality, and specifications of the SIPs produced. It integrates quality assurance into the production process, reducing defects.
- Cons: The initial setup cost is higher, and while the production rate is impressive, it typically doesn’t match the output of traditional laminating facilities for the same investment.
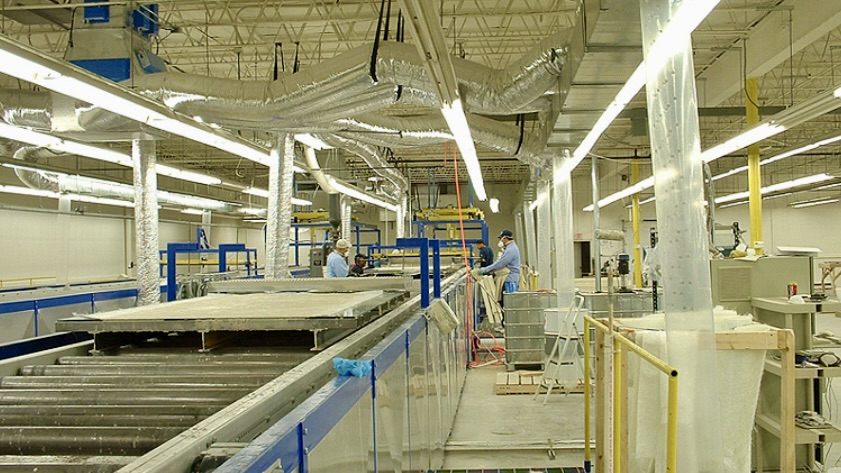
Visual Insights: The images attached to this post illustrate our dual production lines in action, showcasing the machinery and the panels being produced.
Conclusion
Each method has its place in the construction industry, depending on what you’re aiming for in terms of cost, production speed, and panel customization. While the traditional laminating method remains a staple for its high throughput, our integrated approach offers unique advantages in terms of control and customization.The future of SIP manufacturing looks promising, with potential for even more efficient and environmentally friendly construction solutions.
Setting up a SIP manufacturing? don’t hesitate to contact us.
Contact